© Theegarten-Pactec GmbH & Co. KG
BHS packaging machine for bouillon cubes and tablets
The absolute top performer is the BHS for pre-formed cubes, which boasts a total output of up to 3,000 packaged products per minute. The BHS for double cubes manages 2,500 packaged units per minute, which corresponds to the considerable quantity of 5,000 individual packaged products per minute. The BHS for pre-formed tablets also processes 2,500 packaged products per minute.
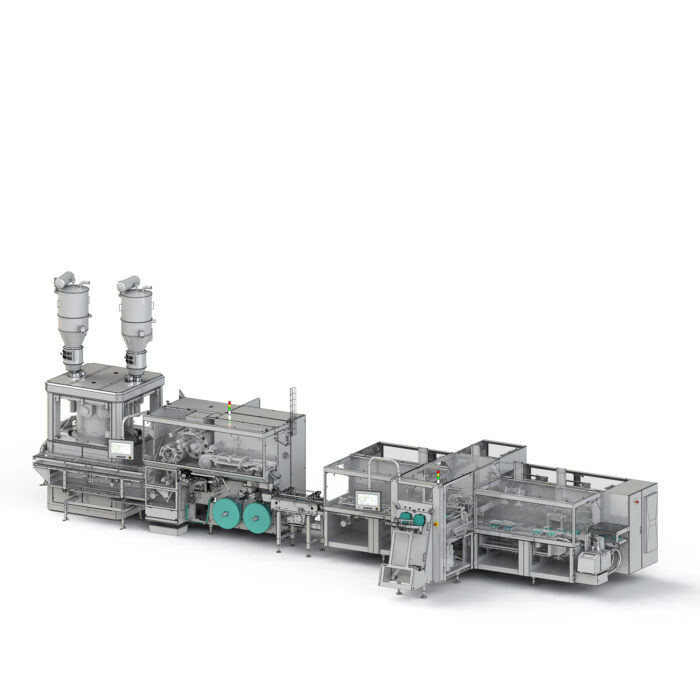
Simple integration Minimal workforce, maximum cost-effectiveness
In addition to its high output, the new BHS also scores points with customers on account of various other advantages offered. For instance, the BHS can be connected to existing presses for the manufacture of bouillon cubes and tablets from granulated foodstuffs without any problem. One production operator is sufficient for the operation of a line consisting of a press and a packaging machine. If the lines are positioned very close to one another, one employee can even operate two lines. In the case of the machine variant for the packaging of bouillon cube tablets, whereby the BLM cartoning system from Theegarten-Pactec can be connected, one production operator is again sufficient for the operation of the entire line consisting of a press, a BHS packaging machine, and the BLM cartoning system.
In addition to manageable staffing levels, numerous benefits also mean that the new BHS remains particularly cost efficient throughout its entire product life. The system incurs barely any maintenance costs on account of the packaging machine requiring no lubrication, while oil changes are required at most once per year. What’s more, the BHS impresses with 50% lower energy consumption per packaged product when compared to other packaging machines.
The ability to track machine parameters in real time makes predictive maintenance much simpler, thereby minimising the risk of fault-related downtime. And the packaging specialists have also reduced the duration of required downtime to a minimum: with the BHS, entire assemblies can be easily replaced; flexibly and quickly. Production continues to run efficiently with the secondary unit while maintenance is performed on the replacement unit.
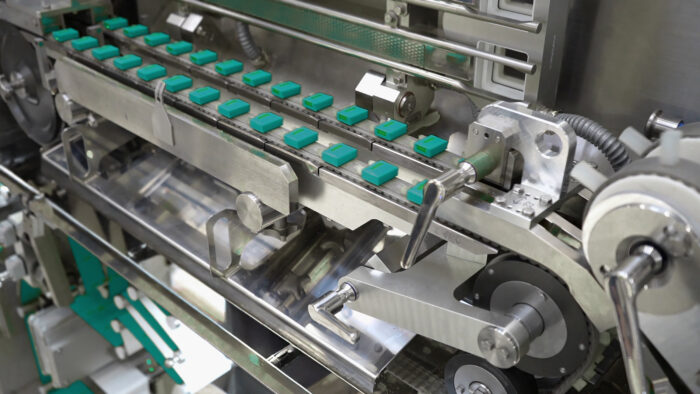
Reliable quality control Guaranteed product quality
The efficient quality control ensures that faulty products are reliably sorted out prior to the packaging process, and insufficiently packaged products afterwards. Pre-formed bouillon cubes or tablets that are too soft on account of an incorrectly configured pressure within the press, the height of which does not comply with the specified parameters, or that are incorrectly positioned on the conveyor belt are identified as flawed. As a result, no products that could negatively influence efficiency or packaging quality reach the packaging process. The camera-based quality control system screens out already packaged products. This also applies if the printed image is incorrect or the folding is distorted, or if the packaging is poorly sealed (for example if it has protruding, open flaps).
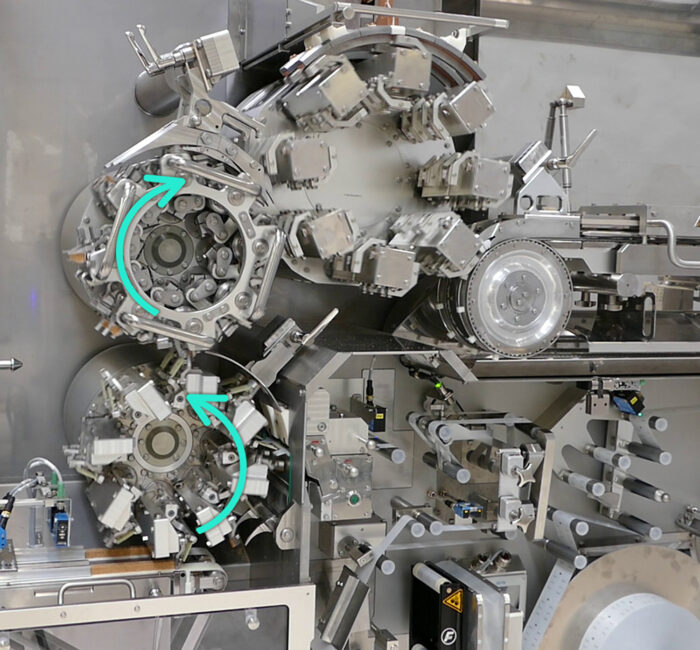
Better hygiene Improved machine design
Each product is only gripped once while unpackaged, thereby significantly reducing potential product abrasion. The unpackaged bouillon cubes and tablets are also gripped in the lower section of the packaging process. Abraded particles produced as a result of contact with the conveyor belts and the product grippers fall downwards. Because the packaging process is carried out upwards, abraded product particles do not make it into the packaging. Furthermore, each product is wrapped in packaging material just 80 milliseconds after having been gripped, which also minimises abrasion. Added bonuses regarding the “hygienic design” of the BHS are the paint-free design of the entire product area, the consistently implemented balcony construction and the large panel elements that grant optimal access to the process by means of a simple pivoting motion.
Theegarten-Pactec Stepping into the future, with the right development partner
We are already in the process of further optimizing the new development. In the long term, both the BHS for double cubes and the variant for pre-formed tablets will also be capable of packaging 3,000 products per minute. What’s more, we are already planning the extension of the system’s range of applications to include, for example, the packaging of powdered milk tabs and cubes, as well as confectionery products.
However, pioneering developments such as these are only possible thanks to the customers’ commitment and cooperation. In this regard, we have invested our long-term experience and a great deal of technical expertise. Innovation naturally entails significant development costs. We are more than happy to make this investment on account of the strong customer demand. We are the ideal partner for manufacturers that are pursuing clear objectives. Together, we are breaking new ground to continuously improve the packaging process.