Despite various crises, rising costs and inflation, consumers still attach significant value to environmentally friendly packaging. According to the Sustainable Product Packaging study published in June 2023 by global consultancy Simon-Kucher & Partners, as many as 62% of consumers in Germany are prepared to pay more for sustainably packaging products, up to an additional 7%. Yet, despite this willingness on the part of consumers, confectionery brand manufacturers looking to adopt more environmentally friendly packaging face challenges in other areas. This is because more sustainable materials often present a challenge in the packaging process.
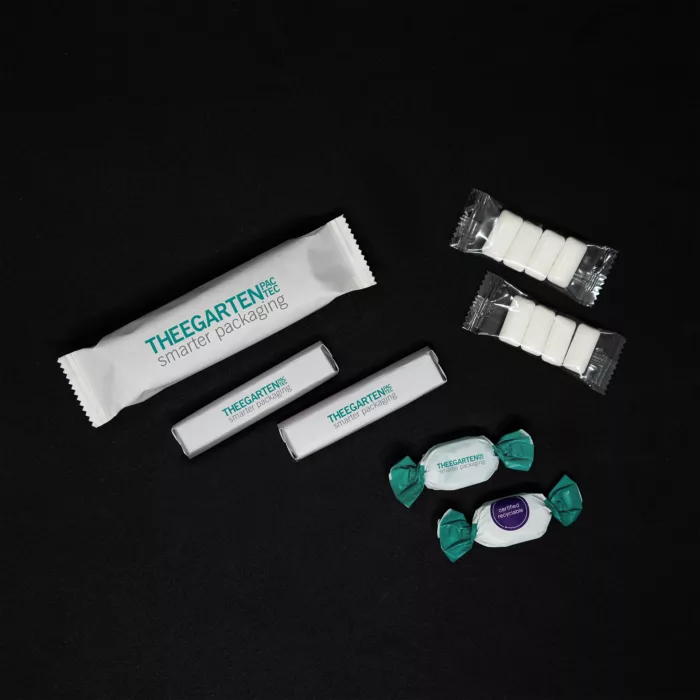
Sustainable materials: recyclable but demanding
Conventional packaging involves laminating different materials such as plastics, metals and papers together to achieve an optimal combination of strength, flexibility and a barrier function to protect the product. When it comes to sustainability, however, these laminated materials present a problem: they can be difficult or even impossible to separate and thus cannot be recycled. At present, mono-materials and paper-based packaging materials are among the most commonly used alternatives and are said to offer better recyclability. However, such materials pose greater challenges during the packaging process. They can tear more easily, are more difficult to seal and sometimes have inferior folding properties.
Theegarten-Pactec aims to support producers and brand manufacturers in their quest for improved sustainability. The specialist in small-sized confectionery packaging from Dresden, Germany, is constantly developing and refining its machines with a systematic focus on processing sustainable materials at industrial scale.
Patented pre-heating device for paper-based flow packs
Theegarten-Pactec has, for example, re-engineered the FPC5 – its high-speed packaging machine for chocolate bars– to such an extent that it can now process paper-based flow packs in the conventional cold-sealing process as well as in the far more complex heat-sealing process. In fact, the machine is capable of producing flow pack packaging with integrated heat-seal capability and a pure paper content of at least 95%.
By pre-heating the seal area during the wrapping material unwinding process, the paper has a higher starting temperature, which significantly reduces the required duration of heat application by the sealing tools to the packaging in the sealing process itself. This avoids damaging the packaging and the product and allows them to pass gently through the machine. In addition, the reduced sealing time makes it possible to achieve high processing speeds of 100 m/min for paper-based packaging.
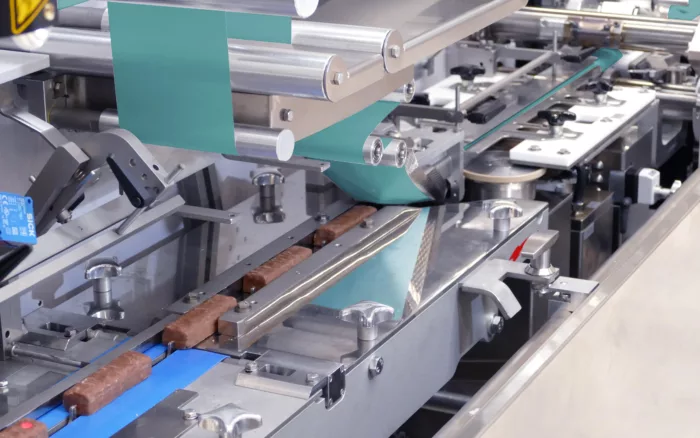
©
FPC5 packaging machine
The specific characteristics of sustainable packaging materials have also been considered in another area: Theegarten-Pactec has modified the forming shoulder for flow packs processing on the FPC5 to support the production of paper-based flow packs. Due to the materials used and the adaptations to the component’s geometry to accommodate the packaging, there is no risk of the paper crinkling or tearing during production of the flow pack.
Recyclable paper processed at high speed in double-twist wrap
Theegarten-Pactec has also addressed the issue of sustainability in relation to its high-speed EK4 machine. Capable of processing up to 2,300 products per minute, it can package hard candy in a double-twist wrap of recyclable, wax-free paper. Despite these high packaging speeds, the EK4 still processes the paper reliably and keeps pace with the processing speeds for conventional foil wraps.
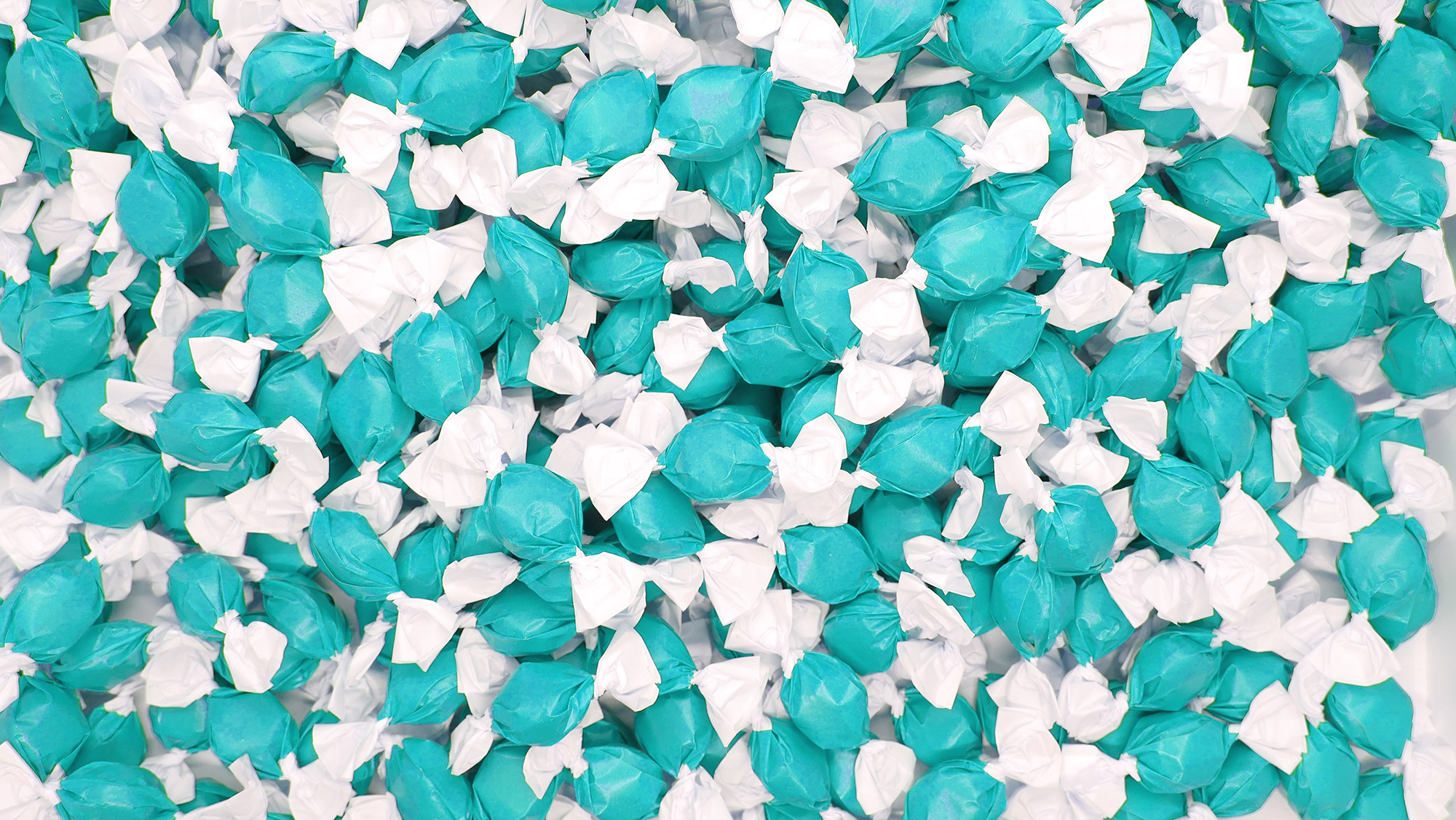
Hard candies in paper
It facilitates flexible processing of wax-free paper and other innovative packaging materials, including through infinitely variable adjustment of twist gripper oscillation. The twisting angle can also be adjusted. Furthermore, different models of twist gripper are available for efficient processing of different packaging materials. The EK4 also works with exceptionally high material efficiency, which further enhances its sustainable credentials. For instance, a servo-driven wrapping material feed roller ensures that precisely the right amount of material is pulled out, thereby minimising material consumption. With the EK4, the packaging specialist demonstrates that it is possible to use recyclable, wax-free paper without compromising either performance or product protection.
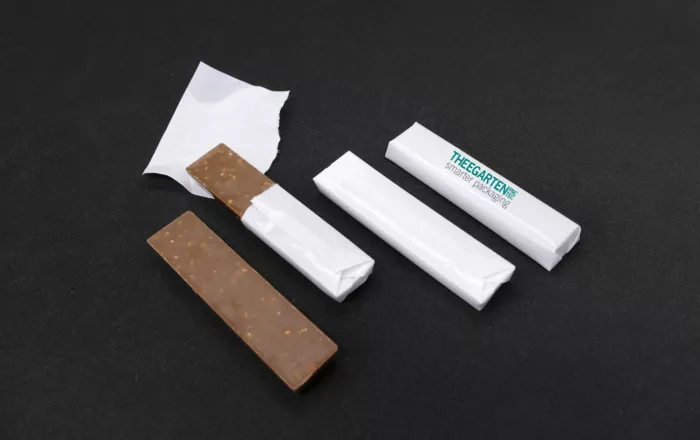
Environmentally friendly packaging of chocolate products Suction-supported sealing
In relation to environmentally friendly mono-films, Theegarten-Pactec has developed a special process: suction-supported sealing. The idea behind this invention was inspired by the poor dead-fold characteristics of recyclable mono-materials, which means that packaging has to be closed after folding, either through sealing or using adhesives. However, such approaches risk damaging delicate chocolate products. With this in mind, Theegarten-Pactec developed a sealing station positioned immediately after the actual wrapping/packaging process.
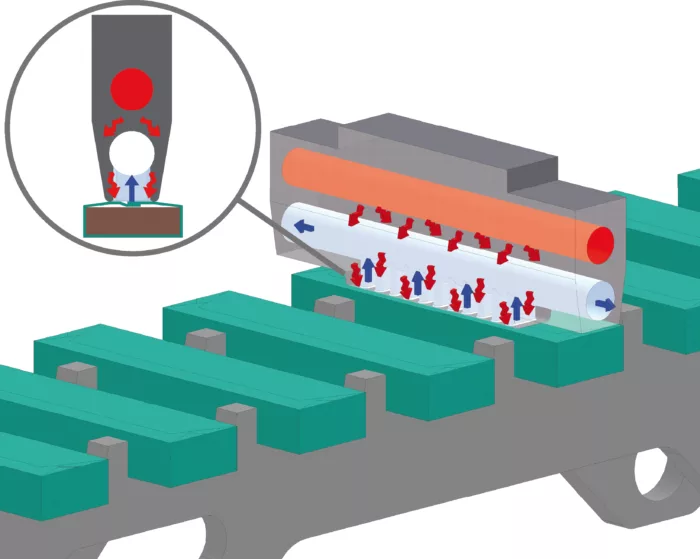
Method suction-supported sealing
As soon as a product reaches the sealing station, the sealing tool moves to a distance of 0.5 mm to 1 mm from the product to be sealed before negative pressure is used to suck the packaging onto the sealing stamp. This process avoids direct contact between the packaging and the chocolate product during the sealing process, thereby eliminating the risk of pressure marks or other damage to the product. Active cooling of the ambient air provides additional product safety.
Markus Rustler, CEO of Theegarten-Pactec, says: “The examples above clearly demonstrate that there are many different areas in which we can take targeted action to improve sustainability. We are constantly striving to refine our machinery in the interests of both the environment and our customers. Ultimately, only by facilitating industrial processing of sustainable packaging will it be possible for such materials to become established extensively and around the world.”